【研氢】绿色合成氨产业发展现状与展望
发布时间:2025/05/08 18:05 来源:中国氢能联盟 分享:
绿色合成氨(以下简称“绿氨”)被认为是潜力极大的传统化石能源替代燃料,其生产过程可实现零碳足迹。目前我国合成氨行业主要采用哈伯-博施法(Haber-Bosch)工艺,所需氢气大多来自传统化石能源制氢,氨合成环节需保持高温高压环境,全生命周期会产生大量的碳排放。绿氨主要是通过绿氢替代和绿电供能,取代传统化石能源供热供电供氢,实现生产过程零碳排放。由于氨相对较高的能量密度、易液化、易储存等特性,推动氨的燃料化利用获得广泛关注。
氨为无碳化合物,其燃烧热值较低,但其能量密度超过了氢和甲烷燃料;且空燃比低,辛烷值高,抗震抗爆性能好,在航空、航运发动机中作为燃料应用具有可行性,并具备较大的市场潜力。
目前全球范围内积极布局绿氨供应链,加速验证氨作为低碳燃料在工业尺度条件下生产应用的可行性。生产方面,根据国际肥料工业协会(IFA)数据,目前全球已开工建设的绿氨项目产能达350万吨/年,远期规划项目产能达7500万吨/年,主要分布在澳大利亚、阿曼、中国、德国等国家。据中国氢能联盟研究院统计数据,截至2024年底,我国在建的绿氨项目产能约190万吨/年,规划绿氨项目产能约1780万吨/年。应用方面,掺氨发电领域,全球燃煤掺烧氨技术处于示范到小规模应用阶段,中国、日本等正逐步扩大机组容量规模。国家能源集团已实现600兆瓦大容量燃煤发电机组20%掺氨燃烧;东方锅炉、皖能集团等多家企业也在探索掺氨燃烧技术应用。氨燃料船舶方面,据挪威船级社(DNV)数据,2024年,全球氨燃料船舶订单总量达27艘,绿氨逐步进入低碳船用燃料市场。当前阶段绿氨主要指通过使用绿电、绿氢替代传统合成氨工艺中的化石能源,采用哈伯-博施法制备的氨。全球超过90%的氨是通过哈伯-博施法工艺生产,所需氢气大多来自传统化石能源制氢,同时氨合成环节需保持高温高压环境,会产生大量的碳排放。利用可再生能源供能开展的电解水制氢及空气分离制氮气,再通过哈伯-博施法制成的氨,其生产过程在理论上可实现零碳足迹。国内可再生能源电解制氢合成氨技术已处在工业示范阶段,但仍面临技术迭代、成本控制等方面的挑战。除哈伯-博施法外,低温低压、光/电催化技术作为合成氨新型制备技术正处于试验研发阶段。低温低压合成氨技术是在催化剂的作用下,在较低温度(≤300℃)下合成氨,包括AMV合成工艺(节能氨五工艺法)和LCA合成工艺(Leading Concept Ammonia,1988年英国 ICI 公司提出)。其中AMV合成工艺合成环境低温低压,可选用低温低压的铁-钴基氨合成催化剂等;LCA合成工艺吨氨能耗低,流程短,转化率高,且合成时也低温低压,可选用铜基催化剂等。光/电催化合成氨直接催化空气中的氮气产生氨气,但由于方法技术难度高,且目前存在转化效率低,成本较高,使用寿命短等问题,尚处于实验室研发阶段。氨储运方面,整体供应链技术成熟,中短距离通常以液体形式,通过公路和铁路罐车运输,大多数采用全压式常温槽罐;远洋或沿海长距离运输一般采用冷冻型氨运输船,船上配备制冷设施来处理蒸发氨气。储存方面,目前液氨运输储罐有冷冻型、半冷型、全压型三种类型。其中冷冻型和半冷型储罐设有保冷和氨蒸发气回收系统,一般适用于大容量储存。全压型储罐是在液氨无保温和制冷条件下的储存方式,一般采用球罐或水平圆柱形卧罐结构,设计压力一般高于1.8兆帕。绿氨较传统合成氨最主要的差异在于氢源,氢源价格是影响绿氨成本的最大可变因素。以15万吨/年绿氨项目为例,生产运行假定条件为:(1)年运行时间按照8,000小时计算;(2)绿氢原料成本20元/千克,氮气成本取0.11元/标方,电力成本0.3元/千瓦时,工业用生产水和循环水分别为4元/吨、0.05元/吨;(3)定员80人,人均工资15万元/年;(4)项目运营期15年。在不考虑碳资产收入情况下,绿氨平准化单位成本将近4,200元/吨,氢气成本约占总成本的86%。随着未来绿电、绿氢价格逐步下降以及碳交易市场普及,绿氨价格较传统合成氨将逐步具备竞争性。绿氨制备成本中绿氢成本占比相对较高,氢价达到约12-15元/千克时可实现传统合成氨的规模化替代。相对于传统合成氨,绿氨项目可获得额外的碳资产收入,碳市场价格每上升100元/吨,对应可降低绿氨成本约为200-420元/吨。绿氨作为新型的清洁零碳燃料可助力能源系统深度脱碳,供应侧合成工艺适应可再生能源波动是发展重点。当前,国内合成氨产线建成年限大多较短,通过产线改造进行原料替代会大幅降低原有产线利用率和生产效益,新建绿氨项目等增量示范模式将成为近期主要选择。中远期,随着产线折旧末期和绿氢绿色效益显现,考虑合成氨的原料气来源独立、耦合操作便利,通过产线改造进行灰氢替代降碳将逐步具备经济可行性,存量替代和增量示范可协同开展。通过科学有序攻关布局,绿氨可逐步实现在氨燃料供应中的主体地位。随着双碳目标的推进与国际碳排放法规逐步收紧,应用侧煤掺氨燃烧将作为重要的能源减碳和安全保障工具有序拓展,船舶与纯氨燃烧需突破技术和基础设施等方面瓶颈。掺氨燃烧方面,需要对燃烧器、进料系统和风管等进行改造。贫氨条件下,氨煤混燃可以协同助燃。当掺氨比例较大时,炉内辐射传热量呈现下降趋势,锅炉尾部受热面的对流传热量则有所上升,需调整燃烧组织或优化受热面布置,避免出现各受热面换热量与设计值偏离过大的风险;掺氨比例升高亦会降低系统效率,可考虑通过入炉空气预热、换热器改造等方法进行优化;此外,烟气组分中水蒸气增加导致烟气酸露点改变,需考虑尾部烟道和尾部换热器的低温腐蚀问题。航运应用方面,以液氨为燃料的船舶需要采取适当的改装和维护。例如,采取对内燃机增压的方式保证氨气燃烧的热值。此外,目前燃料舱、加注及储运等领域技术成熟度较低,存在氨泄露风险;通风系统及电器保护系统技术成熟度不足,存在氨腐蚀风险;基础设施方面,现有的港口不适用于液氨燃料,存在氨泄露和腐蚀风险,需要新建或进行适应性改造。绿氨的规模化推广应用需加强供应侧和应用侧核心技术、关键零部件和材料的创新与突破。供应侧需开发新型低碳合成氨工艺,提升催化剂等材料性能,提高能量转化率,降低绿氨制备成本。应用侧需面向氨稳定燃烧、尾气氮氧化物控制等,加强技术研发与试验,支撑氨燃料的规模应用推广。持续深化技术攻关,采取从化石燃料掺氨燃烧过渡至100%氢气+氨气燃烧,从低碳内燃机逐步发展为零碳内燃机等路径,支撑我国基于可再生能源的“绿氨”技术持续研发,助力能源、交通等行业深度脱碳。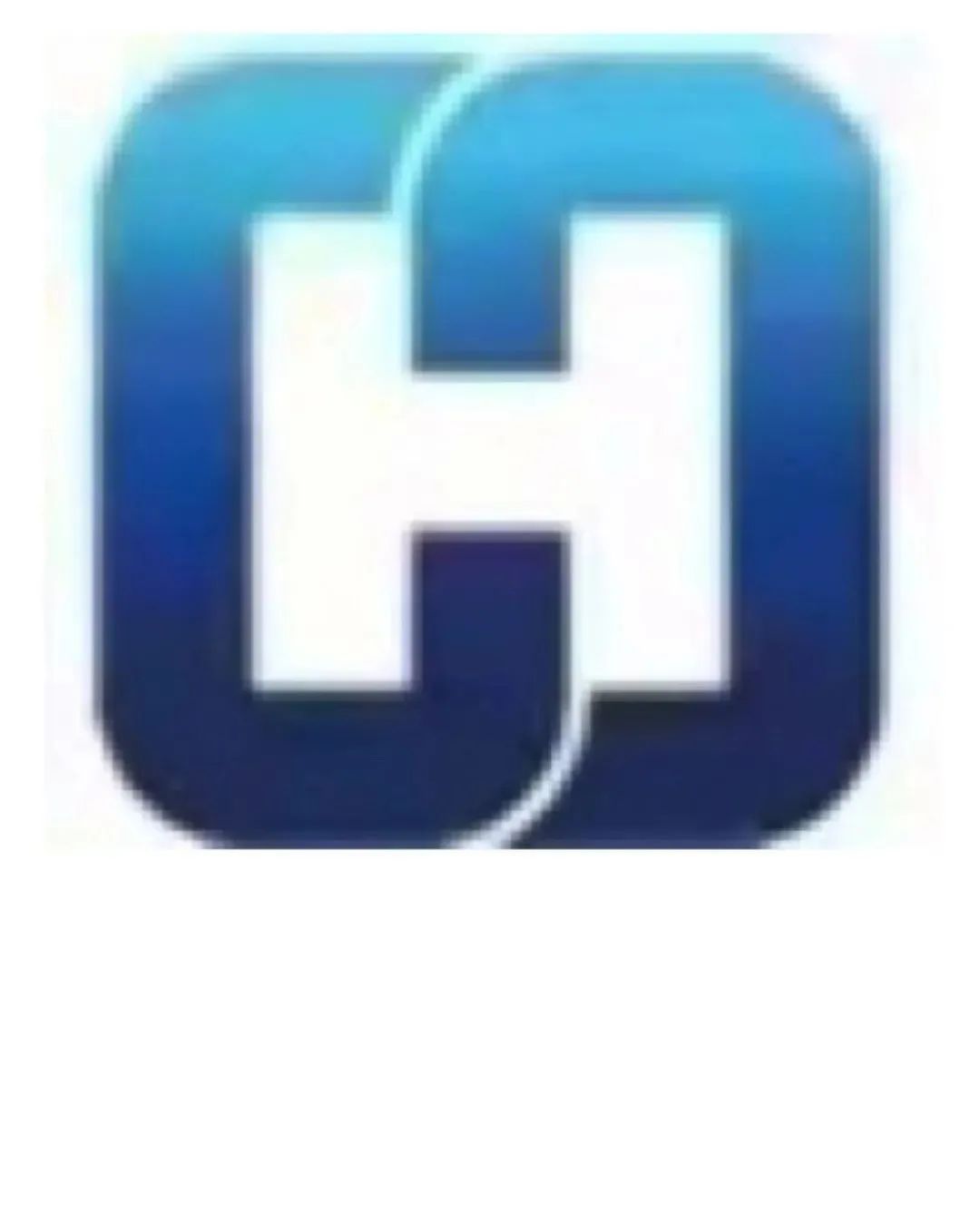
![]()